The Benefits of Aluminum Casting
Aluminum casting offers a wide range of benefits that make the process perfect for most manufacturing applications. It’s common for engineers to turn to aluminum alloys as they create new designs, and even the military uses this method.
The wide range of uses for aluminum casting begs the question what are the benefits of this process that make it so popular? Read on to find out about the benefits of Aluminum Casting.
Versatility: One of the reasons so many designers seek out Aluminum Castings Near Me is that this casting method is exceptionally versatile. Aluminum casting can be used to produce just about any form in any size, shape, or configuration that can be imagined. From tiny electrical components to transmission casings for cars, aluminum casting can be used to produce parts to meet precise design requirements with little need for finishing.
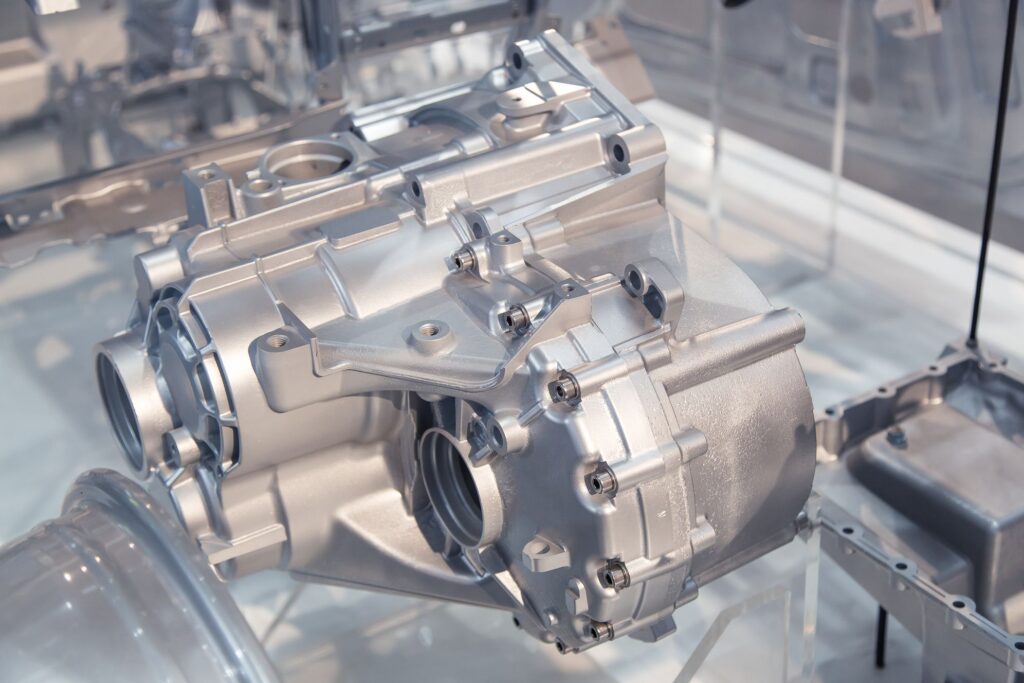
Rate of Production: Manufacturers are always looking for more efficient methods of producing goods. Automation and computerization have helped to speed up some parts of the process, but without the right casting method, this can create a bottleneck. Aluminum casting is a fast process that produces workpieces, parts, and components faster than casting with any other type of alloy.
Strength: Aluminum cast parts offer a strength-to-weight ratio that exceeds any other alloy or metal. Some aluminum grades are stronger than steel grades, and parts made from aluminum alloys can deflect up to three times as much as their steel counterparts when subjected to the same loads.
Appearance: Aluminum isn’t just a popular material because of its impressive strength-to-weight ratio. It’s also aesthetically appealing, which makes aluminum perfect for applications where people will see the finished workpieces. Unlike other materials, aluminum doesn’t need to be re-engineered.
Cost-Effectiveness: Manufacturers need to keep costs low, but they can’t do so at the expense of quality. Thankfully, aluminum casting produces high-quality products even when the process is performed quickly. The cost savings associated with aluminum casting are due primarily to the production speed associated with this process and the elimination of finishing post-production. Aluminum also tends to be less expensive than other metals, which offers even greater savings.
Corrosion Resistance: Most metals become corroded when exposed to adverse environmental conditions. Aluminum, on the other hand, oxidizes when it’s exposed to the air. The oxidation process helps to prevent corrosion and improve the reliability and longevity of cast aluminum parts, components, and products.
Choose a Reliable Casting Company
Whether the part will be placed into an automobile or used to house sensitive electronics, it’s important that every detail be right. Dies, molds, and forms must be designed with precision, so the company must have impressive machining capabilities.
A reliable aluminum casting company will be able to employ multiple casting methods, including not just popular die casting but also less prevalent processes such as sand casting and will have someone available to help customers choose alloys and answer any questions. Don’t settle for a sub-par casting company. Work with industry leaders to get the best results.