Unveiling The Mystery of DTF Transfer Paper
DTF transfer paper is one of the consumables for DTF printers nowadays, and it has the same function as DTF film.
Why do we need to produce DTF transfer paper when we have DTF transfer film?
As the earth is the home of human beings, the resources are always limited, and the recycling rate of DTF PET film is much lower than that of DTF transfer paper, so DTF transfer paper is very necessary to be one of the common consumables for DTF printers in the future.
In the next section, we will introduce the related contents of transfer paper.
1. Easy peeling degree of DTF transfer paper
Some customers feel that the peeling power of DTF transfer paper is big, some feel that it is almost the same as that of DTF PET film, what is the situation?
The peeling force of DTF paper is related to the temperature of hot stamping, when the temperature of hot stamping is too high, the peeling force will be bigger, for example, when the actual temperature of the hot stamping board is higher than 160℃, the peeling force is on the rise, the suitable temperature of hot stamping for 80g semi-transparent DTF transfer paper is 145-155℃, the peeling force will be big when it is too high, and if it is too low, the color of hot stamping will not be bright enough and the fastness of it will not be good, the user can make his own decision according to the characteristics and requirements of the fabrics.
Users can adjust the temperature according to the characteristics and requirements of fabrics.
The peeling force of DTF transfer paper for different shapes of graphics is not the same, pattern edges and sharp corners of the peeling force is small in order to ensure that the details of the pattern; graphic plane uniform peeling force is greater than the hot stamping film, which is the characteristics of the DTF paper decision.
Summary:
(1) The peeling force of DTF transfer paper is directly proportional to the temperature of hot stamping, and it is recommended that the actual temperature control of hot stamping board is 145-155℃;
(2) The peeling force of DTF transfer paper in order to keep the details of the pattern at the edge part of the pattern is small;
(3) The peeling force of DTF transfer paper in the pattern plane is larger than that of hot stamping film (but smaller than that of traditional inkjet thermal adhesive transfer paper).
2. Color fastness of DTF transfer paper
The color fastness of DTF transfer paper generally refers to three situations, one refers to the dry and wet rubbing fastness of the hot stamping picture, the second refers to the bonding fastness between the skin layer of the hot stamping picture and the fabric, and the third refers to the hot water washing fastness.
It should be pointed out that DTF paper and hot stamping film is only the medium that carries the image printed by the coating ink, which has little relation with the color fastness itself.
The biggest factors affecting color fastness are:
①Hot melt powder adhesion amount
DTF transfer paper and DTF films are both printing media, but the ink absorption capacity is different, DTF paper’s ink absorption capacity is higher than DTF Transfer films, so when printing DTF paper generally do not need to be heated in the printer desktop and into the dithering machine front plate heating, because the ink is dry, will make the adhesion of hot melt powder.
Because the ink drying will make the adhesion of hot melt powder decrease, resulting in the color fastness decrease when the adhesion ability with the fabric is not enough when hot stamping.
②Temperature and time of hot stamping
The temperature of hot stamping is transferred to the hot melt powder through the transfer paper, because the thermal conductivity of 80GSM DTF transfer paper is smaller than the traditional hot stamping film, the temperature of hot stamping can be a little smaller than the hot stamping film, it is recommended not to apply the production temperature and time of DTF film completely, you can do a small trial with the same fabric before the formal hot stamping production, and then produce after getting the temperature and time of hot stamping with satisfactory color fastness.
The hot water washing fastness mainly lies in the material of hot melt powder, please choose the suitable hot melt powder for the hot stamping apparel which requires heat-resistant washing.
3. Printing arching and wind-absorbing wrinkles
The obvious difference between DTF transfer paper and DTF PET films is that its medium has the effect of water absorption, so it is easy to make the paper fiber absorb water and deform when printing water-based ink.
At present, SUBLISTAR has optimized the structure of hot stamping original paper, which makes the wet deformation of the original paper very small and solves the problem of printing arching.
In addition, DTF transfer paper is not as stiff as DTF film, so in the process of printing, please pay attention to minimize the suction force of the printer table, especially when stopping the printing, please turn off the suction of the table, so as not to leave the section of DTF paper on the table to be suction wrinkled.
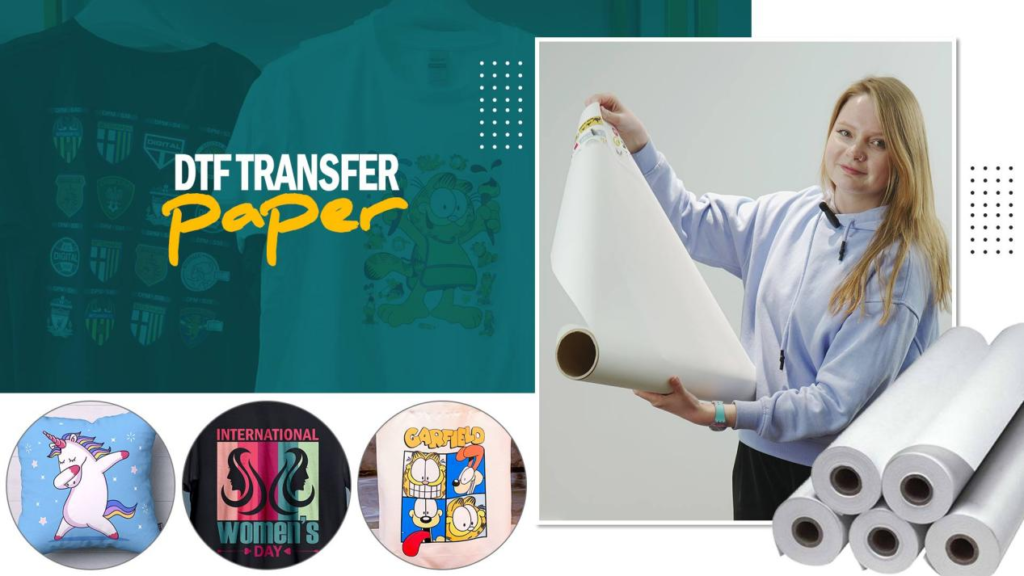
4. Will DTF transfer paper also stick to powder?
DTF film has the annoying problem of hot melt powder adhering to the graphic blank, will DTF transfer paper also stick to powder?
Many trial users have this concern.
First of all, please understand the two reasons why DTF transfer films stick to powder: one is caused by the cationic adsorption of anionic hot melt powder on the coating; the other is caused by the static electricity of PET film.
The former occurs when the environmental humidity is high, and the latter occurs when the environmental humidity is low.
Due to the absorbent nature of the paper there is no need to rely on strong positive lock anionic ink, DTF paper coating is close to neutral, but in the case of high ambient humidity there will be some sticky powder phenomenon, such as this situation, please pay attention to reduce the ambient humidity (such as turning on the air conditioning dehumidification function) or enter the shake powder machine before the guide plate slightly heated to remove moisture.
Another situation is in the edge of the graphic sticky powder, the solution is to shrink the white ink graphic appropriate, so that the edge of the color map is drier and not sticky powder.
5. Oil return of hot stamping image
Hot stamping image oil phenomenon is caused by the glycerin in the coating ink, we add different amounts of glycerin for the coating ink in the experiment, the sample hot stamping image into the 95% RH humidity box, it can be clearly seen that the glycerin content of the ink image of the return of the oil is obvious, the glycerin content of the less almost no return of the oil.
The experiment shows that DTF transfer paper and DTF films have similar situation, but DTF paper will perform slightly better due to its absorption.
We see that some DTF PET films have increased the amount of powder on the surface of the film in order to reduce the sense of oil return, but more powder will affect the performance of the color of the hot stamping, and it is not good for the strength of the coating, and it is inconvenient for storage and transportation and preservation.
The above is the explanation of some status of DTF transfer paper.
We will continue to add the later technology and content updates.